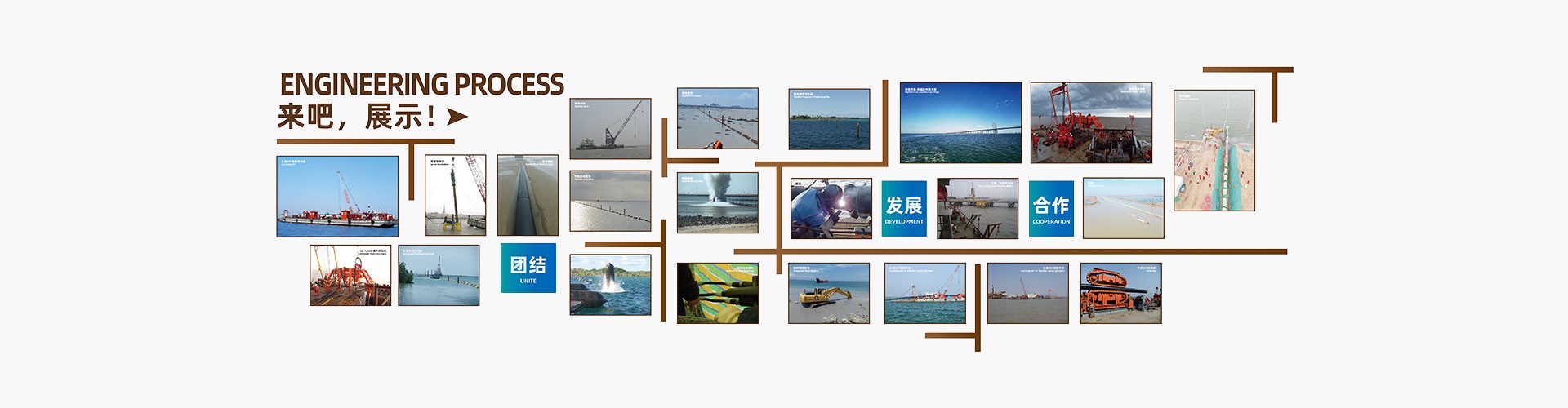
The submarine pipeline is called the energy vessel, which shows its importance. So, how is such a long pipeline under the sea connected? An Offshore Cable Repairing Service Provider.
We robots know that pipes are metal. Corrosion is inevitable in the Underwater Pipe Laying. In fact, the corrosion of pipelines is mainly external corrosion and internal corrosion. The so-called corrosion is the phenomenon of surface damage and weight loss caused by the physical, chemical and electrochemical effects of the surrounding medium on the metal surface.
Historically, major accidents caused by pipeline corrosion are believed to have been heard by everyone. Once the pipeline is laid, the corrosion will not only bring high maintenance costs, but the losses will be huge. Therefore, it is important to prevent the corrosion of pipelines.
The weak point of pipeline corrosion is at the interface. In order to ensure the safe operation of the submarine pipeline during the design life, the pipeline system should fully prevent internal and external corrosion caused by the transmission medium and seawater.
Outer coating, engineering practice has proved that in actual seawater environment, the outer coating can provide effective corrosion protection. The outer coating for submarine pipelines includes coal tar enamel, asphalt enamel, epoxy resin, polyethylene resin, polybutylene rubber, etc.
Cathodic protection, as a supplement and reinforcement of the outer coating, cathodic protection can provide sufficient protection during the design life of the submarine pipeline system. The cathodic protection system of submarine pipelines is usually based on sacrificial anodes.
The material of the sacrificial anode may be an alloy of aluminium or zinc. The weight and number of anodes are related to the resistivity of the surrounding soil, current density requirements, coating damage standards, and pipeline design life. In the design, the weight of the anode, the distribution distance, the length and thickness of each pole piece should be calculated. On coated submarine pipelines, the distance between the two anodes generally does not exceed 150m. The shape of the anode has a long shape, a plate shape and a semi-ring shape.
The installation method of the anode on the pipeline should ensure that it will not be mechanically damaged during the loading and unloading and construction of the pipe. The diameter of the anode block should be smaller than the diameter of the weight layer and should be firmly fixed on the pipe. In order to ensure a reliable mechanical connection and correct position between the anode and the tube, the two half halves can be welded together.
For internal corrosion control, internal corrosion control should be performed on pipeline systems that transport corrosive hydrocarbons. For submarine pipelines, internal corrosion control methods include the use of corrosion inhibitors, adding corrosion allowances, internal coatings, corrosion-resistant pipes or linings to keep the transport medium free of water.
The internal anti-corrosion program is determined according to the nature of the conveyed medium. These properties include the ratio of oil, gas and water; salt content, bacteria content, water pH value; corrosive gas content; solid content and its flow characteristics; temperature And stress.
If you are interested, please contact China Submarine Pipeline Installation.